Customer Success Story : Poclain
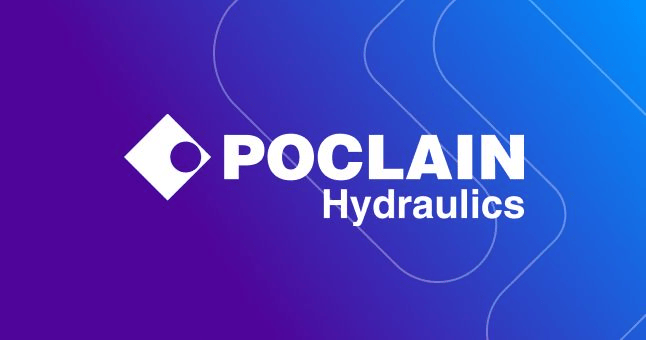
Who is Poclain Hydraulics?
Poclain Hydraulics is a French company that designs and manufactures hydrostatic transmissions based on high performance, cam-lobe, radial-piston motors. With its world-leading technology, the company caters to diverse industries such as industrial, agricultural, construction, material handling, environment, and on-road markets. A broad catalog of mechanical components is accompanied by service offers that span from infrastructure design to after-sales.
Poclain was founded in 1926 by the Bataille family. From the late 1940s to the 1970s, the company was a leading force in the global excavator market due to its innovative hydraulic motor technology and strategic diversification. In 1974, Poclain was sold to Case, and in 1987 the Bataille family officially took over the Hydraulics division, creating Poclain Hydraulics.
Today, with over 2000 employees and 70 years of expertise with hydraulic solutions, Poclain Hydraulics has expanded its worldwide presence with subsidiaries in countries such as Italy, China, Slovenia, United States, India, and the Czech Republic and commercial offices in 13 other countries.
Their Project
The company takes pride in its innovative spirit. “At Poclain I am free to explore new avenues, which is not always the case in an industry like ours. It is not common in other companies that an employee gets to run with an idea without necessarily knowing if it will produce a result. But they trusted me and my idea. We ended up producing something, and today we’re in the process of setting it up industrially” reveals Stéphane Chaperot, Group IoT Architect.
The project he refers to is Poclain Hydraulics’ latest physical machine monitoring application, developed by Stephane himself. The idea for the tool arose from the need to pinpoint and understand possible physical issues that might occur to their hydraulic systems in the field. The application seeks to provide Poclain’s teams with the information necessary to troubleshoot the issues before the machines are delivered to the client. The data collected is also used during the ongoing maintenance of the machines.
“We need to be able to understand the physical risks associated with these types of systems. In order to do so, we must keep records of what happens to them during testing” explains Chaperot.
In their turn, the records are forwarded to engineers, who perform calculations with the data received in order to filter and search for specific events. Events can be classified as pressure peaks, abnormal speed fluctuations, or sudden temperature spikes, for example. From the beginning of their analyses, however, engineers were satisfied to find that more times than not, the identified issues stemmed from product selection in catalog and not from their design. They were therefore usually able to solve the issues by simply replacing a part in the Bill of Material (B.O.M.).
Their Solution
In order to collect the data necessary to monitor the machines, an Electronic Control Unit (ECU) is installed as an IoT gateway and is listening at CAN-bus. This allows them to collect values like pressure, temperature, RPM, etc. from components like hydraulic pumps and motors. These motors are incorporated into the wheels of the machine (a loader, in illustration), and all events that are happening on hydraulic components are recorded.
The ECU communicates with Scaleway’s IoT Hub, automatically sending real-time data. From the IoT Hub, the information is then sent to a “file monitor” application that listens to the messages and stores them in Object Storage. The team is currently setting up lifecycle rules on Object Storage to determine when an object should be sent from the “Standard” class to “Glacier”, for long-term storage.
A “file decoder” application fetches information from Object Storage, decodes it, and sends the data to an instance running Influx-DB, a time-series database. Calculations are performed with Influx-DB and another part of the data is consulted using Grafana, which runs on a different instance. Grafana allows the engineering team to visualize signals such as the path traced by a vehicle, its speed, and pressure distribution. These pieces of information allow the team to look for the elements causing issues on the hydraulic motors.
The “file monitor” and “file decoder” applications are developed in Node.js, and each one, as well as the Influx-DB and Grafana nodes, is hosted on its own GP1-M instance.
Scaleway’s Asset
During the initial stages of his project’s development, Stephane Chaperot took his time to search for different infrastructure solutions online. He stumbled upon Scaleway’s different virtual instance offers and, because he knew the company and trusted the Iliad Group, decided to test them out.
Satisfied with the results, Chaperot decided to attend the first edition of ScaleDay, Scaleway’s groundbreaking event, in June of 2019. There, he was able to meet the developers behind the products and was introduced to Gregoire de Turckheim, Scaleway’s IoT, Edge & Automation Product Manager, who unveiled all the possibilities of the Scaleway IoT Hub, which was in its Beta version at the time.
“I’m really glad I met Gregoire. He is wonderful. He has always made himself available whenever we needed to discuss our project.” reveals Chaperot. He goes as far as extending the compliment to all of Scaleway “Every time there’s a problem, there’s a level of reactivity and response that is really good. It is really fabulous to work with this level of motivation which, often, comes from people who are passionate. You will have trouble finding it at bigger companies, where you usually go through many steps before finding the right person to talk to”.
Chaperot and his team really like working with the Scaleway console, as they find it intuitive and user friendly. They nonetheless plan to automate their deployment process by using more of Scaleway’s APIs down the line.
In the near future, they will rely more heavily on the multi-cloud so as to benefit from PaaS solutions offered by other providers, such as Azure and AWS. This does not mean their infrastructure at Scaleway will downsize. On the contrary, Poclain Hydraulics is currently working with an outside specialist to set-up a Kubernetes Kapsule infrastructure to host their applications in an easily scalable and cost-efficient environment. As far as data processing is concerned, in the first quarter of 2021, Poclain counts on processing their data using Python on Scaleway GPUs.